Lightweight Design of Glass Bottles-production Process Control
- Share
- Issue Time
- Dec 10,2021
Summary
You can read this article to learn more about how to control the lightweight design of glass bottles from the perspective of production technology, so as to more clarify the structure and characteristics of glass bottles.
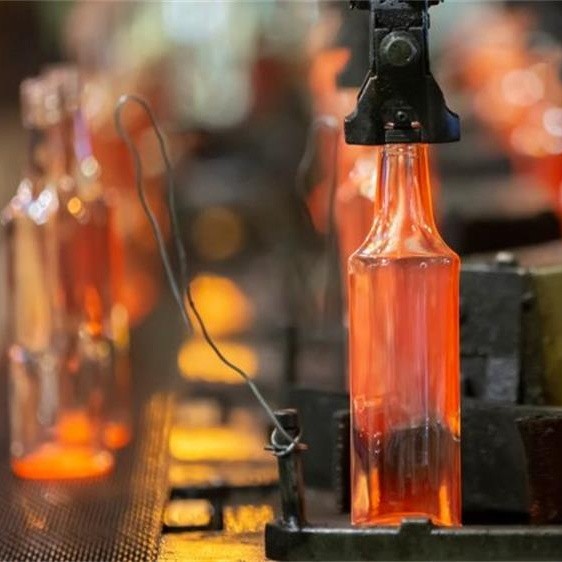
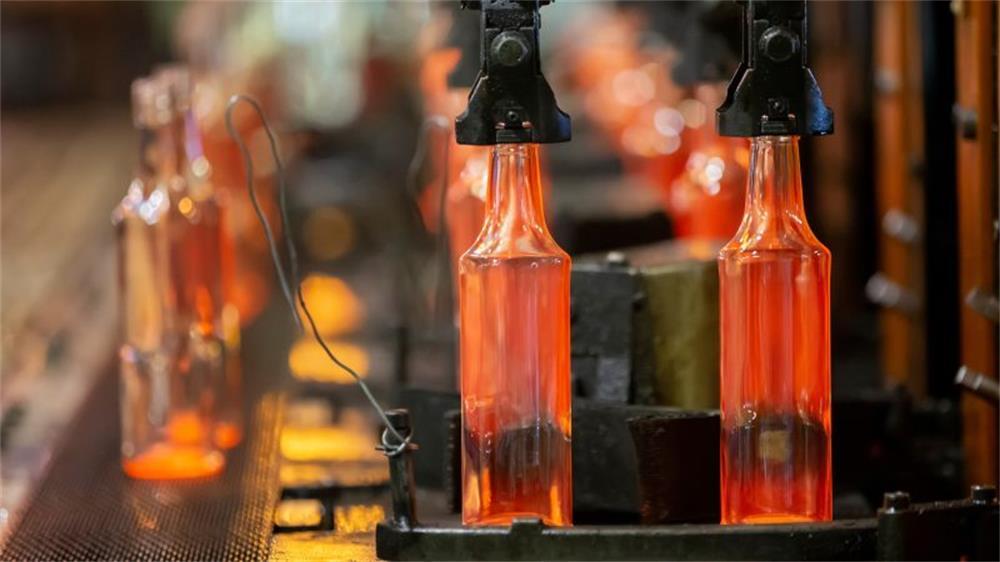
The lightweight of the glass bottle is to reduce the weight-to-volume ratio of the glass bottle under the condition of ensuring a certain strength, and the purpose is to improve its greenness and economy. The weight-to-volume ratio is a measure for evaluating the quality of glass bottles with the same volume. According to different uses, the weight-to-volume ratio of light-weight bottles is generally between 0.15 and 0.8.
The weight-to-volume ratio of lightweight bottles is small, and the bottle wall is relatively thin. light. The wall thickness of the lightweight bottle is 2~2.5mm on average.
Reducing the weight-to-volume ratio of glass packaging containers mainly depends on reducing the wall thickness. However, it is very difficult to maintain a high compressive strength in a thin-walled state, and it is necessary to start with all aspects of the whole process from design to production.
Through glass composition modification, reasonable structure design, correct process arrangement, effective production process index control, effective surface treatment, and other strengthening treatment measures, the goal of small wall thickness and high strength is achieved. This article mainly discusses with you how to control the lightweight of glass bottles from the aspect of the production process.
1. Doing a good job of ingredients is the first step to achieve lightweight production
The formulation design of the raw materials and batch materials preparation process, the composition of the raw materials, the particle size, the moisture content, the uniformity of the batch materials, the quality of the cullet, and the uniformity of the addition all have a direct impact on the product quality.
To do a good job of ingredients, we must implement stable formulas, formulate and strictly implement raw material standards, and institutionalize the preparation of ingredients. The production of high-end lightweight bottles pays special attention to this link.
In terms of production weighing and accuracy, the batching system adopts advanced computer-controlled electronic weighing equipment, and the dynamic accuracy should reach 1/500 to ensure the quality of the batching.
2. The melting process is not only to ensure the quality of glass packaging, but also a key link in the green glass packaging
The glass melting process can be roughly divided into five stages: silicate formation, glass formation, clarification, homogenization, and cooling. The melting process adopts continuous operation, these 5 stages are carried out in different parts of the furnace, so as to control the accurate melting temperature in sections. The stability of the kiln operation process index is very important.
Generally, it is required that the melting temperature fluctuation does not exceed 10°C, the liquid level fluctuation does not exceed 0.5mm, and the kiln pressure fluctuation does not exceed 2Pa to prevent fire in the furnace space, thereby preventing quality problems such as stones, color, appearance, and poor strength.
In the production of high-end lightweight bottles, the requirements for the accuracy of the distribution channel temperature and the fluctuation accuracy of the glass level are very high, and some are controlled within ±2°C and ±0.2mm respectively.
Of course, to ensure high-precision production process indicators, it is necessary to promote oil-fired kilns, improve kiln types, and use high-temperature, wide-section, large-scale roller-type horseshoe flame furnaces.
A series of measures such as full heat preservation, bottom bubbling, electric boosting, kiln sill, and microcomputer control of thermal parameters are implemented for the kiln so that the melting rate can reach 1.5 to 2.0 (t?m-1), and the melting quality is significantly improved.
3. Effective molding control is the guarantee to obtain the expected molding effect and uniform wall thickness
The process of producing glass products from molten glass can be divided into two stages: forming and setting. Molding and setting are continuous. During the molding process, it is necessary to control the viscosity and temperature of the glass, as well as the heat transfer through the mold to the surrounding medium.
Glass containers usually control the forming operation from three characteristic temperature values: softening temperature, annealing temperature, and strain point. For different products, it is the key to determining reasonable parameters through experiments. Advanced bottle making, feeding and heating systems, and the use of advanced molding processes are the fundamental guarantee for achieving uniform wall thickness and achieving lightweight.
4. Implement effective annealing to eliminate harmful residual stress
Annealing glass bottles and glass jars is a heat treatment process that eliminates or reduces the residual stress in the glass to an allowable value. Any glass product has residual thermal stress or permanent stress during processing. In order to eliminate these thermal stresses, the glass needs to be heated to the annealing point for heat preservation and soaking, so that the internal structure of the glass can be adjusted and the stress released.
The annealing process of glass includes 4 stages of heating, heat preservation, slow cooling, and rapid cooling. We must accurately control the heat preservation time according to the wall thickness, and during the slow cooling stage, we must strictly control the cooling speed to avoid new stress. In the rapid cooling stage, different cooling speeds should be used according to the wall thickness to prevent the temporary stress generated during cooling from exceeding the strength limit of the glass and causing cracking.
DAS Packaging realizes the lightweight of glass bottles by controlling the production process, and takes into account its quality, and can also provide users with a variety of options. If you want to learn more about related services, you can send us your needs, and we will give you a satisfactory answer as soon as possible.
As a professional glass container and packaging manufacturer, we have won praise and trust from many customers with our excellent manufacturing technology and thoughtful one-stop shopping service. Our products are sold all over the world and used in all walks of life. We also have a professional quality inspection system and provide comprehensive customized services. If you are interested in our glass bottles, please contact us immediately!